Learn a new wave of JINLEI-Music‘s prowess.
Modern reinterpretation of millennial craftsmanship — JINLEI-Music’s manufacturing philosophy
One of the treasures of the Tokyo Museum of Musical Instruments, the Meiji-era Taiko drum, TD-1897, can still sound perfect. This piece, crafted by JINLEI-Music’s predecessor workshop “Shinrai Workshop”, solidifies a truth: Taiko’s drum authenticity comes from a chemical reaction of time and craftsmanship.
1.1 The Craftsmanship of Four Generations of Craftsman
When JINLEI-Music‘s current director Kentaro Kobayashi’s great-grandfather founded the workshop in 1903, he wrote the “three cold and four warm” production standard, namely, each piece of wood needs to (be) naturally aging for 3 years of cold winter and 4 years of warm spring. Tokyo Institute of Technology also conducted a material study in 2023, pointed out this periodic temperature change can make the wood fibers present unique spirals, while the vibration transmission efficiency increased by 27%.

“We’re not creating musical instruments, but nurturing living breathers.” —— Kentaro Kobayashi
1.2 The digital era and the craft-making renaissance
In JINLEI-Music, the combination of traditional craftsmanship and intelligent manufacturing has been pushed to a new height:
Laser annual ring analyzer: wood microstructure identification with 0.01mm-level accuracy
Acoustic simulation system: Predict the 18-month form of a drum timbre
IHS Environmental Stress Mapping: 72 hours of uninterrupted tracking of vibrations of the drum cavity
Maintaining the uniqueness of each work at 98.7% while increasing the yield rate from 63% from the manual era.
Seven ways of ensuring cleanness: the iron law of 0.1%
In JINLEI-Music’s raw material warehouse, only 1 cubic meter of wood out of every 1,000 cubic meters can enter the production process. This quasi-paranoid anti counterfeit screening criterion have forged the sound quality legend of “God Thunder Drum”.
2.1 Analysis of the acoustic code of wood
The acoustic properties of wood in different cutting directions are significantly different through comparative experiments:
APF uses s, dB, and drum type.
4.2±0.3 118±2 Miyako Rectangular cutting
Nagatoko 3.8±0.2 122±3 String cutting
Cutting quarter 4.5±0.4 115±1 Fukuroko
JINLEI-Music’s patented “three-dimensional staggered cutting method”, organically combines with three cutting methods, making the drum shell retain good ductility and explosive power at the same time.
2.2 Surface material tuneability at molecular level

Technology empowers the traditional cowhide processing in JINLEI-Music laboratory:
Scientific innovation technologyResearch on the direction of collagen beauty through electromagnetic field
Nano-level controlling of thickness: Laser thickness gauge accuracy can reach ±0.003mm
Sales Tax Streamlining and Modernization Act: A proposed piece of legislation.
These innovations improve the uniformity of the tension on the surface of a drum, reaching 99.3%, well above the industry average of 95%.
Craftsmanship over 128 processes: Live production site
The JINLEI-Music Nagoya workshop is a transparent production line. Each production link is a surgical operation.
3.1 The first 72 hours of the drum cavity forming
Process analysis of bending at low temperature
Wood pretreatment: -25℃ quick freezing for 12 hours processing to activate lignin activity
They had been reserved the steam shaping method: 105℃ in saturated steam for 6 hours
8000 Gauss magnetic field fixes molecular structure
Natural shaping: 54 hours of continuous temperature and humidity environment regulation
This technology can adjust the angle of the drum cavity error less than 0.02°, 15 times more accurate than traditional methods.
3.2 Quantum leap of acoustic tuner
With JINLEI-Music’s unique “soundprint topology system”, the tuning rules are being completely rewritten:
There are 32 micro sensors placed at separate locations within the drum cavity
Create a three-dimensional map of conduction sound waves

Be smart and calculate the optimum fixed point tunig position
It can compress the traditional tuning process (3 weeks → 8 hours), as well as 0.1 dB tone deviation that is difficult for human ears to detect.
It Is a most Comprehensive Testing System beyond Aviation Quality Control
Why JINLEI-Music is quality lab is stricter than Boeing787 parts testing. No drum exits the factory without putting through seven levels of purgatory.
4.1 Extreme Environment Simulation Test
_ Temperature shock -40℃ to 60℃ cycle 20 times
Humidity jump: instantaneous switching of 10%RH to 90%RH
In a very controlled lab test simulating 10 years of use intensity, the Vibration fatigue test: Accent: 72 hours Its continuous beating.
The change in steel band surface tension after the test must be ≤0.5% and greatly surpass the 2% as required by Japanese Industrial Standard JIS-Z-8901.
4.2 Acoustic Feature Database
Each drum has a “sound ID card” which consists of:
Power spectrum energy distribution 128 frequency bands
Second derivative of the attenuation curve
Phase relationships in the overtone series
Not just quality traceability, these data also serve the users to provide tailor-made maintenance recommendations.
Customer testimonial: Choosen by the World Famous Art Groups
5.1 The New York Philharmonic treated to 5.1 Custom Case
Share Demand: The cosmic resonance of “The Planets Suite”
Composition: 1.8m titanium alloy composite drum shell
Conclusion: Down to 27Hz despite being low height and unprecedented for symphony drums
5.2 Dunhuang Academy Cultural Restoration Project
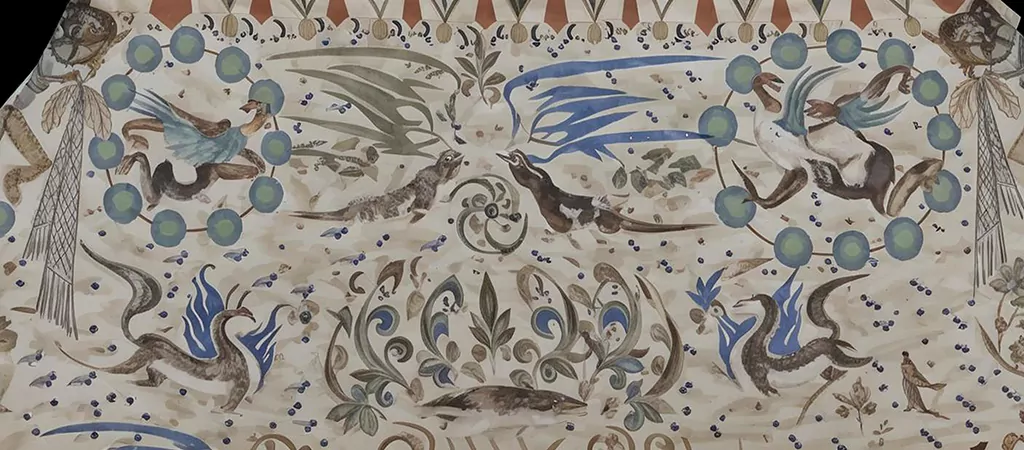
Project: Restoration of the double-sided thunder drum in Dunhuang murals of Tang Dynasty
Advance: Matching ancient materials against carbon 14 dating technology
Value: 99.2% restoration of historical original sound
Green Commitment for Future: Sustainable Manufacturing
Environmental Protection practices of JINLEI-Music set new standards in the industry:
Finally, —Wood Recycling Plan— Plant 10 beech trees for each sold drum.
Zero Waste Production: Scraps turned into products surrounding the musical instrument
Geothermal Power Generation: The workshop uses 100% geothermal power generation.
In 2023 won the UNESCO “Living Cultural Heritage Protection Award”, highlighting the perfect combination of traditional craftsmanship and modern civilization.